Why is methanol the favoured middle ground when it comes to high performing motors, especially of the supercharged variety? Greg Gower is the crew chief on Craig Glassby’s formerly world record holding alcohol funny car. He said there are several reasons racers favour alcohol (of the fuel variety) and we got him to explain what racers should think about in considering methanol as a fuel.
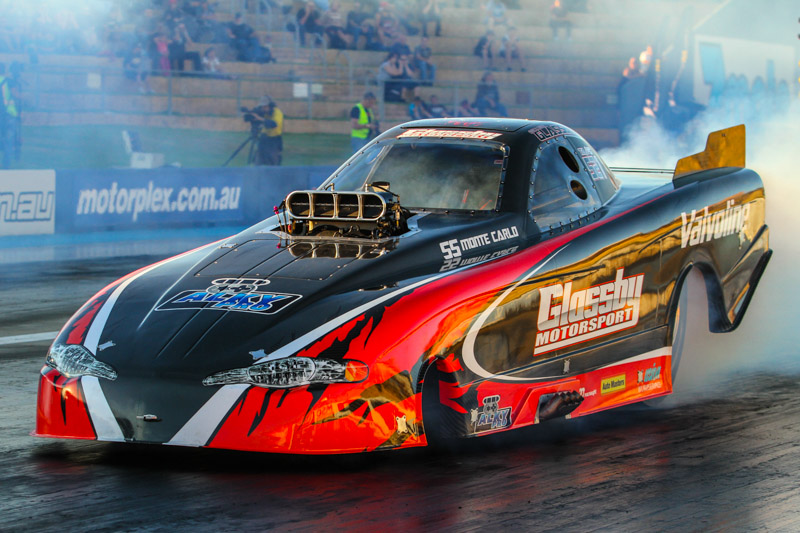
“Methanol has a strong cooling effect on the air coming into the engine, so if you can keep the intake temperatures down you can run a lot of compression and a lot of boost,” he said. “It also carries some oxygen which you don’t get with petrol or gasoline, but no where near as much as nitro.
“A secondary effect we get on these blown engines is that some of the excess fuel we use cools the combustion chamber and valves, which also suppresses detonation. Because we run constant flow injection, fuel builds up behind the intake valve when it’s closed. On the Hemi engine, the valves are close together and directly across from one another, so during valve overlap a slug of air moves through the chamber and out the exhaust, and it carries a lot of that fuel buildup with it.
“There is the fact you can run so much cylinder pressure and get away with it. It will just detonate and destroy itself on petrol with high cylinder pressure.
“What drag racers do with alcohol engines is crazy, we run compression ratios in the 10-12:1 ratio area and we are running 50-60 pounds of boost. The guys in the states with the C-rotor PSI superchargers are running 60 psi or more.”
The benefits of methanol aren’t just in boosted applications. Gower said the cooling effect also applies to a naturally aspirated motor.
“As a general rule, methanol makes about 10% more power,” he said. “But it depends on the engine combination, it’s often much more than that on a heavily supercharged application. Methanol engines generally make more torque than a petrol engine and they also make more horsepower because of the cooling effect and the oxygen content.”
The importance of volume in the fuel system
To take advantage of the power increases methanol can offer, it does require a much higher volume fuel system. Gower said the ballpark figure is about 2.5 times more fuel than the same motor using petrol.
“If you look at the calorific value, petrol is higher than methanol and that leads some people to say petrol is a better fuel,” he said. “But it doesn’t take into account the oxygen in methanol or the cooling effect, the cooling increases the air density in the cylinder.
“One of the other myths is that it is often accepted is that methanol burns slower than petrol and you need more timing. That is wrong. If you do your homework and look at the flame propagation rate it burns faster than petrol. People get the idea because sometimes engines are so rich they see flames coming out the exhaust.
“To make best use of methanol, a higher compression ratio is advised to take advantage of its cooling effect and high octane.”
Because of the beefed up flow requirements, converting an engine to use methanol means looking at every aspect of your fuel system – not forgetting that you will need a much larger fuel tank and a substantial air vent.
“Everything has to be up to it,” Gower said. “You have to make sure nothing in the system will be affected by methanol because it attacks certain components – they will swell or break down because of methanol. It’s rarely a problem with race components, but for a street/strip car you need to make sure any seals, gaskets or hoses are compatible.”
Another effect of running methanol that a lot of racers will see is milky oil.
“This is just a build up of methanol in the oil, mainly seen when the engine is rich,” Gower said. “Blown alcohol engines are run rich at idle to control temperatures. Fuel gets past the rings into the sump, and drag engines don’t run hot enough or for long enough to evaporate it out.”
The secrets of tuning methanol
When it comes to tuning a motor using methanol, Gower said it can be a forgiving fuel if you stay on the rich (fat) side.
“You can be 10% rich and the engine will still run fine, but it will start to make more power as you get closer to where it wants to be,” he said. “If you get too lean it can be fairly destructive.
“Because methanol makes more power when rich it is more forgiving than petrol. With a decent blower you can still make good power running rich where it is safe and happy and you are never going to hurt anything. The guys that need to be more competitive keep a close eye on it.”
Gower explained some of the physical signs that teams look for in a motor to determine how rich or lean it is running.
“What we look for on the spark plugs is that when you start to make high temperature in the cylinder (an indication of running leaner) it starts to burn the cadmium on the spark plugs; it starts to go white,” he said. “First you will get a little bit of white, then it will start to spread around the plug and you can get an idea when you are getting close and which cylinders are richer or leaner than others.
“When a cylinder is making a lot of power or you are maybe starting to get some detonation it will spread the upper rod bearings a bit. We measure the spread with a digital vernier, it’s only thousandths of an inch.
“Finally it’s important not to forget that other factors play a part in all this. The configuration of the fuel system, how the plugs look, how the engine comes apart and so on, are also affected by the clutch, the track, drive ratios, the engine combination (heads, camshaft, compression), ignition timing and more.”
Drag racing is rife with tuning myths and tips that might work for one engine but not another. Gower said that to understand what is happening to your engine on a pass you need to understand how the fuel system works.
“A common mistake is not understanding where the fuel goes, for example how the flow of fuel is affected by boost in the manifold,” he said. “The fuel you flow into your engine is fighting against the boost you have in the manifold and you often end up flowing less fuel than you think you are putting in.
“I’ve seen people tuning with spreadsheets that calculate the orifice areas in the system, but they’re not accurate due to these differential pressures.
“There are also racers that don’t use any tuning software or calculations and they tune by methods such as when the air changes by 500 feet you change the pill by a certain number. That stuff really doesn’t work because every fuel system is different. That pill size change on one engine doesn’t have the same effect as on a different engine and the flow change is not linear in relation to the pill numbers – that is, the flow change in going from say an 80 to an 85 pill is quite different to going from a 120 to 125 pill, even though both changes are five pill sizes. It’s flow area and pressure that matters. There are a lot of myths like that.”
Better air conditions will result in more power, but the change is less than than that experienced by a petrol-fuelled engine.
“If the tune-up is corrected properly, the fact that methanol cools the air so much means the cars aren’t as fussy,” Gower said. “And this is a key to tuning them because the evaporation of methanol changes the air the engine sees.”
Using software to help tune
Many teams use software to help them tune their set up and Gower said that not understanding how the software works or not setting it up properly initially is a problem. It’s an issue he has tried to address by developing his own tuning software package – Alky Pro.
“I have gone into teams to help them and looking at how their tuning software is set up and it’s often not right,” he said. “One of the things I have tried to do with Alky Pro is lay it out very logically so that racers can understand the fuel system better, they can see what everything is doing and if there is something wrong they can pick up on it.
“Good tuning software performs a number of tasks. It will calculate all the flow areas in the fuel system, the differential pressures and the total system pressure. It also calculates the air density based on current ambient conditions (temperature, humidity and barometric pressure) and provides the correct main jet the engine needs under those conditions. Finally it should be able to calculate what the jets or solenoids that many racers use for fuel management are doing at any point on the race track.”
Gower’s software takes the calculations a step further, using a methodology developed by US engineer Patrick Hale.
“We know the air entering an alcohol engine is drastically cooled by the injection of methanol,” he said. “In effect, these engines have chemical intercooling, so the air entering the engine is not what we’ve measured in the pits. Patrick’s method calculates the change in air density that occurs, and the result is a more accurate correction factor.”
Knowledge is power, and in drag racing that saying is quite literal. Gower said people should not be afraid to ask others for advice in setting up their fuel system to run methanol as it is a well trodden path.
“The knowledge is available to run it, all the components are available. Just start rich and keep an eye on the engine and plugs,” he said. “Of course, there is a wide variance between a blown Outlaw car and a Top Alcohol car, there is a big range in between there.
“The TA guys and the AA/FC guys are revving the engines a lot harder, that gets into areas where you have to watch out for fuel pump cavitation. This happens when the gears in the pump are demanding fuel so quickly that the fuel can’t fill the cavity created by the gears fast enough, and once the pressure drops below a certain point (the vapour pressure), you get cavitation and it creates a bubble which then collapses immediately. It can affect the flow of the pump at high RPM. You will see a slight drop off in fuel flow on your data. It’s dependent on pump design and a lot of people modify pumps to raise the RPM at which it occurs.”
Fuel pump choice is vital and Gower explained the options available.
“When it comes to fuel pumps, there are two broad classifications, those with cast bodies and those with billet bodies,” he said. “If you’re using a cast body pump, you need to keep the fuel pressure down, because the bodies aren’t rigid enough and they can lose significant flow at high pressures and RPM. On the other hand, the billet pumps are quite linear up to several hundred pounds of pressure and they’re definitely the best choice. The pump should be flow tested on a good test bench (see an example below) and I believe they must be flowed with methanol.”
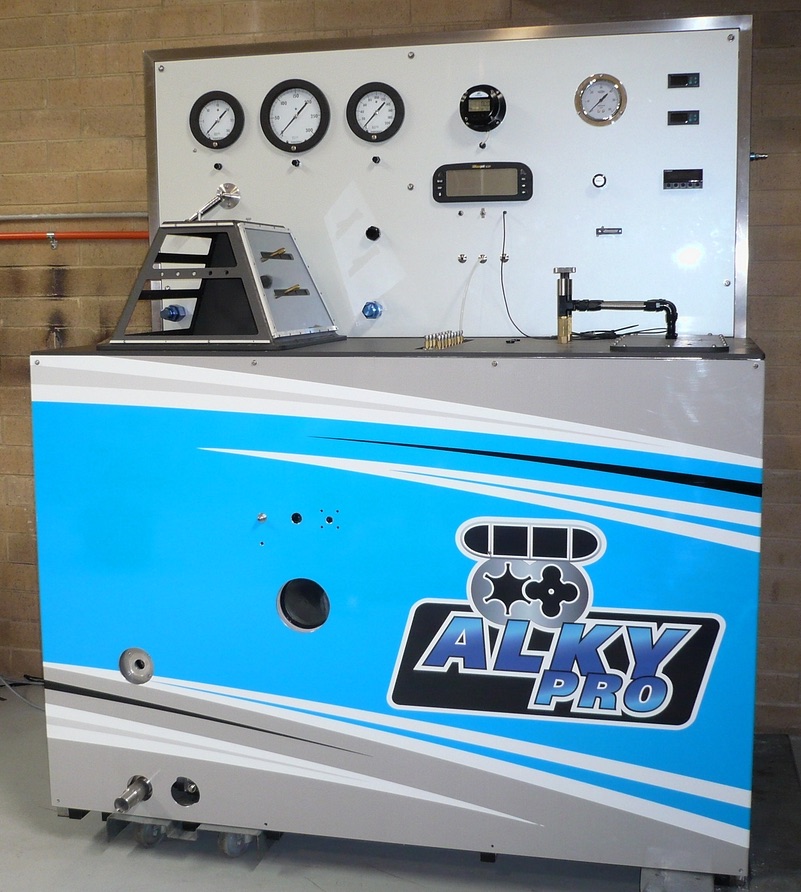
Gower said that racers should flow what they race in order to get the most accurate test of their fuel system.
“Many racers think it’s okay to flow test with water or a flow solvent and then make a correction which they believe gives the same results as flowing with methanol,” he said. “Unfortunately, these liquids don’t have the same physical properties as methanol and it affects the results.
“Viscosity affects the flow of the fluid through the entire system and especially the nozzles and surface tension affects the spray pattern, but the most important property when flowing pumps is the vapour pressure of the liquid.
“Water has a very different vapour pressure to methanol, so you will not see pump cavitation at the same point with water or any other liquid. If you want to know exactly what your fuel pump flows, and whether it cavitates at a certain RPM, it has to be methanol.
“I must add that flow testing with methanol is potentially hazardous and you have to take every precaution against a fire or explosion if you go this way.”
Continuing Gower’s pro level tips, he advised against trusting the turbine flow sensors used on many cars.
“I’ve been told they are calibrated with water and after using them for many years on different race cars I’ve found them to be pretty inaccurate,” he said. “The shape of the graph will be okay, but the actual numbers can be out by quite a bit. In order to trust an on-car turbine flow sensor, it should also be calibrated on a flow bench using methanol.”
At the advanced end of methanol tuning, such as that kind required to run a 5.410 second pass in an alcohol funny car, there are many tricks that start to get employed. We got Greg to spill just a few of the beans on what people are up to and what has changed since he and the famed Castrol Top Alcohol Funny Car team ran the first alcohol five second pass in Australia in 1993.
“There’s a lot of guys putting more injectors into the hat to get as much of a cooling effect as they can,” he said. “And one of the big things these days is fuel management. Guys are running multiple solenoids on the fuel system and they are adjusting how much fuel they’re injecting at different parts of the track. That is where the secrets are.
“Back when we were racing and ran the first five in the 90s we didn’t know any of this stuff. It still amazes me we even ran that five. We had a PSI blower with an A or B-rotor, I can’t remember, but it was making about 25 pounds of boost, about half what we are making now. We didn’t have the clutches, we didn’t have the cylinder heads, we didn’t have the knowledge we have now.
“It’d be interesting to know how quick we could have gone back then with good fuel management, but if I could have had one modern item back then, it’d have to be the PSI D-rotor.”
This article featured in Drag News Magazine issue three. Want to see more articles like this each month? Subscribe to Drag News Magazine.